October 13, 2023
- Oil & Gas
- Canada
- Pre-Commissioning
Pre-Commissioning & Pneumatic Testing of Oxygen Service Piping
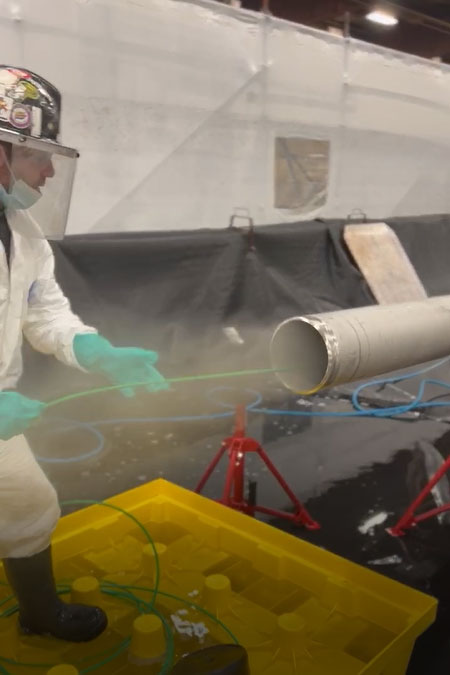
Zero incidents, timely pre-commissioning and pneumatic testing of oxygen lines through clearly set processes, strong technical expertise, and clear communication with the client.
Oxygen service lines have some of the tightest cleaning specifications required prior to commissioning due to it’s reactivity. FourQuest Energy is an industry leading expert in providing this highly specialized service.
The scope of work included:
- Hydro-milling of the spools followed by an engineered water rinse
- Cleanliness inspection using ultraviolet light
- Creation and registration of a Pneumatic procedure with ABSA
- Incident-free pneumatic testing execution
- Air blowing to remove debris contamination during installation and dry the lines down to -40°C dew point
Contamination free wash bay setup
Due to the stringent requirements of cleaning oxygen service piping, a contamination free wash bay was set up. The bay featured side coverings to prevent contaminants from entering and personnel were fully equipped with Tyvek suits to maintain the level of cleanliness.
Pre-commissioning cleaning – hydro-milling
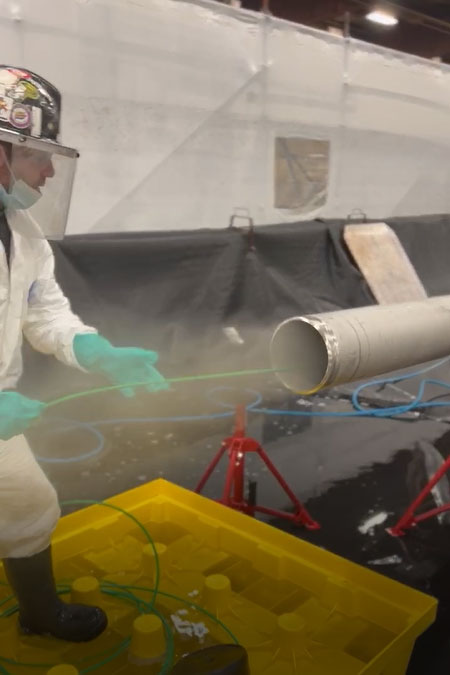
- 143 stainless steel pipe spools received from a fabrication facility were hydro-milled with heated specialized industrial cleaner, followed by an engineered water rinse
- Indoor wash bay allowed for a controlled, clean contamination free environment to perform hydro-milling
- The cleanliness of the spools was inspected with ultraviolet light
- The cleanliness of the spools was preserved by capping the flanges and wrapping them before transportation to the site
Procedure development and pre-planning pressure testing
An execution procedure outlining the equipment needed, injection points, and exclusion zones with the client and ABSA approval was finalized weeks before the job start. A kick-off meeting was planned before the execution to finalize any last-minute changes. Preliminary equipment setup and system tagging catalyzed the job scope execution, leading to the scope finishing on schedule.
Pneumatic testing and line drying
Pneumatic testing using air was performed. As the stored energy in the packages was greater than 1677 kJ, pneumatic testing procedures were registered with ABSA prior to execution. Once the oxygen line’s integrity was proven, the lines were blown out using dry air to bring down moisture content to -40°C.
Both the pneumatic testing and line drying were performed using food grade 100% oil-free air to meet the oxygen line cleanliness criteria.
Advance setup and meetings prior to job execution resulted in on budget and timely execution of the pneumatic testing and air blowing.
From day one, the job was treated professionally. The knowledge and experience of the whole crew was exceptional, from the easy to clean to the difficult components. It never left me how well the crew was at working through difficult problems. They developed creative ways such as swabbing for organics inside the pipe during the pigging operation. Friendly and easy to work with all the way from project management to the people cleaning the pipe and components.
Client Representative
Highlights
Oxygen lines were cleaned and tested safely with zero incidents
Ultraviolet light inspection to inspect spool’s cleanliness
Design of a registered pneumatic procedure with ABSA as stored energy >1677 kJ
Achieved stringent cleanliness criteria for oxygen lines