January 1, 2017
- Power
- Canada
- Chemicals
Bearing Failure in 100MW Turbine
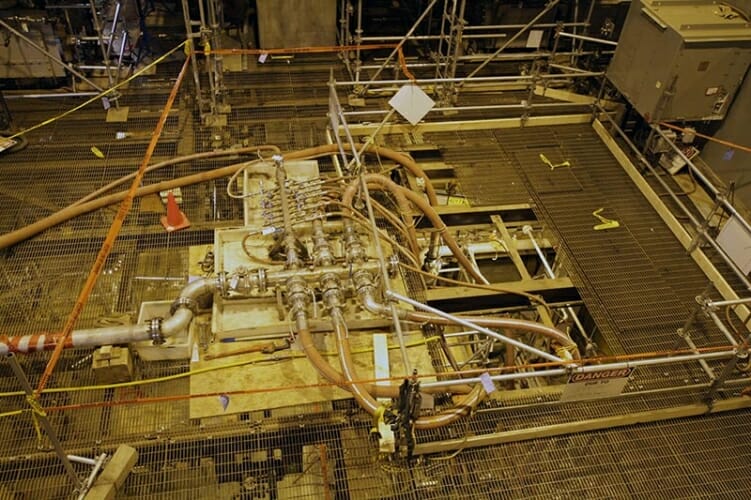
An Alberta power producer had a bearing failure in the 100 megawatt natural gas peak unit turbine.
The required cleanliness and sensitivity of this piece of equipment is comparable to that of a jet engine. The oil within the system was badly burnt and filled with microscopic particles. These particles were not able to be captured by the existing system filters, which were filtering at 3-5 microns. The particles were so small in fact, that they were actually capable of passing an ISO spec, but still the client knew something was wrong with their system.
Our engineers were called in initially to perform an onsite particle analysis of the oil to verify the quality. After thorough analysis it was determined that a full scale chemical degrease and oil flush would be required.
The system was fully drained of the contaminated, burnt oil before a full system degrease was performed to remove all residual oil from the stainless steel system. Upon completion of this stage, the system was filled with new oil for flushing. The system was flushed using 1 micron absolute filters until NAS 5 cleanliness specification was reached. Once the cleanliness specifications were confirmed, the turbine manufacturer drained all the oil from the system and replaced with fresh oil to be circulated by the system filters. Final confirmation of cleanliness was performed and signed off.
Highlights
Client bearing failure resulted in burnt, contaminated oil.
FQE onsite particle analysis determined level of contamination and path forward including chemical clean and oil flush.
System degrease and oil flush were successful at achieving the NAS 5 cleanliness standard.