January 9, 2017
- Power
- Canada
- Pre-Commissioning
Open Loop Lube Oil Flushing
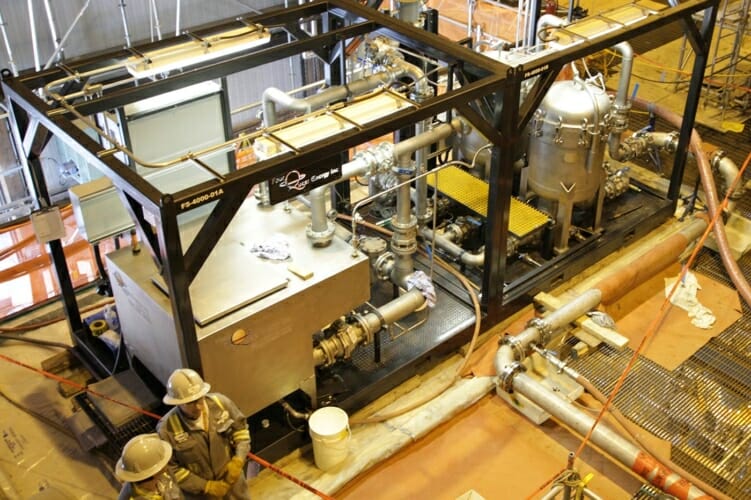
A Saskatchewan power producer required oil flushing on the lube oil system of their steam turbine generator.
A Saskatchewan power producer required oil flushing on the lube oil system of their steam turbine generator. This lube oil system posed a unique set of challenges to overcome. It had three bearing housings that were open to the atmosphere, which provides a significant risk of spills during oil flushing operations.
The pre-engineering for this system needed to be designed to overcome the pressure drop while still maintaining adequate velocity throughout the piping to achieve turbulent flow. Too much pressure would have caused oil to flow out of the open bearing housings on the turbine. Every loop was meticulously designed to ensure the system would surpass client cleanliness expectations without causing an oil spill.
Through the use of our specially designed oil flushing equipment, our personnel were easily able to maintain the very specific flow rate and pressure. Our all encompassing flushing equipment allows us to heat, filter, change direction of flow, and control the flow rate of the oil all from one unit.
The flushing oil was heated to 80oC and flushed at a minimum flow velocity of 3 m/s to achieve turbulent flow in all piping. Pneumatic vibrators were also used to assist in the removal of stubborn debris.
The client required cleanliness specification of ISO 4406 16/14/11 was determined using an onsite particle counter. This was achieved within 9 days of flushing.
Highlights
Open loop system created unique challenges regarding pressure drop and spills.
Detailed engineering was able to account for these challenges
The use of specialized equipment allowed the engineering procedure to be successful executed.