January 24, 2017
- Oil & Gas
- Canada
- Pre-Commissioning
Pre-Engineering of Steam Blows for an Alberta Refinery
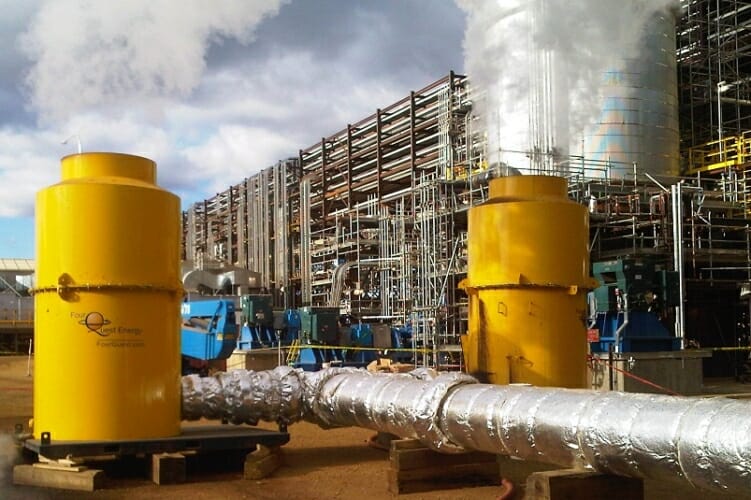
FourQuest Energy engineers were mobilized to a central Alberta Refinery to perform pre-engineering of steam blows for our client.
The initial step consisted of field verification of the system and proposed steam blow points. Based on this field verification, we utilized plot plans and client isometrics to design our temporary piping. Once completed, our procedures were thoroughly reviewed with the client to ensure all parties involved approved of our proposed layout and execution plan. We clarified tasks, ownership, and responsibilities for each company involved (ie. who was providing vac trucks, at temperating water, quench water, etc.).
Our engineers performed the necessary calculations to determine water requirements for the steam blows, a critical component in successful steam blows. These requirements were given to our client for verification of system capabilities, ensuring their system wouldn’t go down in the middle of a blow. For these blows, steam was being used from the main header, which was also providing other operational components with steam at the same time. If our blows, and the usage requirements of the other components was not accurately planned, then either certain units would have gone down due to low steam amounts, or the boilers would shut down (a fail safe operation due to lack of back pressure and flow).
All of this detailed planning meant all permits were already in place, services coordinated, plant utilities were ready, and other trades/vendors were in place when the time came to begin the execution of the steam blows.
Our pre-engineering was able to reduce the overall estimated cost by $68,000 or 40% of the job!
Highlights
Pre-Engineering ensured steam availability was accurately accounted for.
Coordination of all companies, services, and utilities involved.
A reduction of 40% on the total job cost was realized.